What you should keep in mind when modeling before 3D printing.
In practice, often printed 3D models to create a 3D configurator do not look nearly as good in reality as they do on screen.
In order to achieve the highest possible quality of 3D printing, a number of modeling techniques have proven their worth, which we would like to introduce in this article. In detail, we will show you how to avoid the most common mistakes, how materials and 3D technologies influence the printability of a model and how to create high-quality designs.
Preparing for digital development.
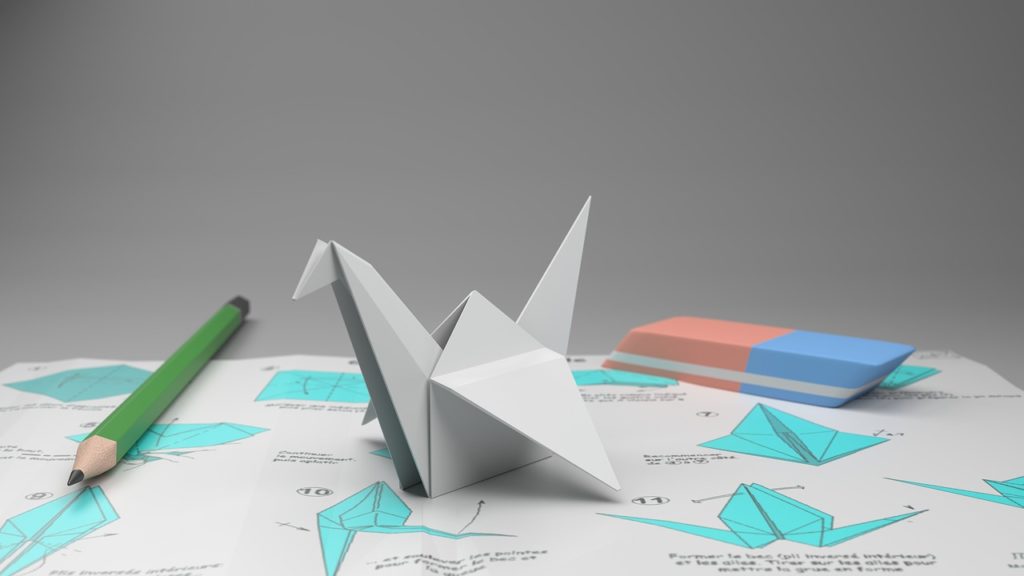
3D models created in a digital environment do not always struggle with physical effects such as gravity or internal stresses at connection points. It becomes critical at the point where you print your model in 3D. Then it becomes a physical object exposed to the laws of nature. Therefore, additional stability should be added to the 3D model.
There are several simple rules that ensure that the 3D model is properly prepared:
- Make sure that all parts of your 3D model are connected within the geometry.
- Make sure your model is waterproof.
- Use a continous flow for the outer surface.
- 3D printing technology & material guidelines.
In the world`s most widely used industrial 3D printing technologies, each printing technology has its own technical limitations and material specifications. In order to optimize for the respective printing technology, it is important to know the requirements already during the modelling.
Use the following basic guidelines to prepare 3D models for specific technologies:
- FDM und SLA technologies require support structures for any overhanging locations.
- Powder technologies generally do not require support structures, with the exception of SLM.
- For SLA and other powder technologies (SLS, SLM, CJP), it is important to install alignment holes to remove the unsintered filler material.
- By hollowing out your model to print on large objects, you save material costs and production time.
- When creating thin and many elements, they can shrink. This is due to the cooling process and the resulting internal stresses.
- A subsequent addition of material to the corners, which can later be removed again, ensures strong adhesion to the outer corners.
- Each 3D printing technology has its own resolution, but usually details smaller than 0.1 mm are not visible after the production process.
- 3D printing also has its own dimensional tolerance, which means that the dimensions of a physical object can differ from those of a digital object. The normal tolerance is -/+ 2% and should always be considered.
Checking the wall thickness.
One of the most common errors with 3D models that are prepared for production preparation are components with walls that are too thin. While in the digital world it is possible to create surfaces without considering their thickness, in the physical world this leads to a variety of problematic results.
Thin elements, especially when merged, can either break, warp, or not provide the durability required to support other parts of the model. For this reason, we advise the user not to design models with elements less than 1 mm thick.
Correct 3D model resolution.
3D printing is based on the interpretation of the mesh representation of objects. This is a series of triangles or other polygons connected by their common edges or corners. When exporting the 3D model and setting triangulation, it is important to set the number of triangles correctly during output:
- Too many triangels can limit or unnecessarily slow down the 3D printing process.
- If too few triangles are used, the result will be a coarse or poor quality model.
- A small outlook.
Additive manufacturing is rapidly expanding the use of 3D printing technology in many industries because it is much cheaper and faster than alternative methods. The use of best practices from the outset and automated processes enable companies to simplify and accelerate their production.
In upcoming blog posts, we`ll give you more tips for high-quality 3D printing.