What you should know about 3D printing in the automotive industry.
A special development in the automotive industry (3D configurators are very popular in this industry) in recent times has been 3D printing. If you seriously believe that the automotive industry is lagging behind in this development, you should read this article carefully. Car manufacturers understand the benefits of using this technology and are even leaders in its application.
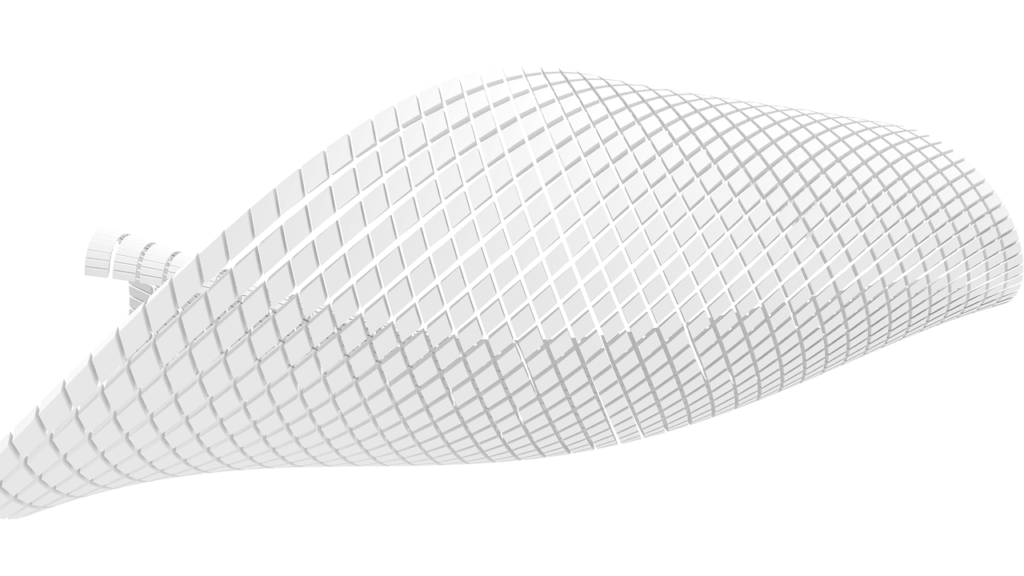
If current trends continue, 3D printing will continue to gain importance in the automotive industry thanks to its past benefits and future innovations using the technology.
Ford.
Believe it or not, Ford has been using 3D printing since the 1980s. So the company can be called an early adopter, because at the time people had no idea it existed. In 2017, Ford produced a total of approximately 500.000 vehicle parts using a 3D printer.
Ford was the first automotive manufacturer to try out the Stratasys Infinite Build 3D printer, taking a big and bold step toward integrating 3D printing into its own manufacturing processes.
This printer is able to create components and even tools of any lenght and shape. It is perfect for producing a prototype vehicle, which can be an expensive and unnecessarily difficult task. In fact, setting up tools for a prototype can take months, while 3D printing can take hours in the worst case. This would significantly speed up vehicle development.
Thanks to the 3D printer, production downtime has been significantly reduced. The broken tools on an assembly line would be quickly and efficiently replaced if they could be printed on the spot instead of waiting hours or days.
In addition, the printer is well suited for components of small series models, including Ford Performance vehicles such as the Ford Focus ST. The cost of setting up tools to manufacture these components is excessive and makes printing financially much more attractive.
Ford sees the growing demand for fuel efficiency, both from government and consumers, as an important reason for using 3D printing. He claims that a printed spoiler could weigh less than half the weight of a conventional cast metal spoiler.
Bugatti.
The French car manufacturer Bugatti is known for its excesses and brings this feature to its use of 3D printing.
Bugatti was the first company in the automative industry to use the Laser Zentrum Nord in Hamburg to rpint a solid titanium brake caliper. The component is still in the testing phase, so full production is not yet in full swing.
The use of printed titanium offers some performance advantages. Bugatti says that the process loses as much weight as possible while maintaining the maximum torsional stiffness. In a panic braking situation, the caliper flex can extend the braking distance, which makes the difference between accident avoidance and crash.
For the Bugatti Chiron, an aluminium alloy brake caliper is first used, which is manufactured using a traditional forging process. The standard front calipers weigh 4.9 kg each. With the 3D printing units, the weight is reduced to just 2.9 kg.
During production of the calipers, four high-power lasers melt titanium dust, which is added by the printer. Again, time is a consideration. According to Bugatti, printing just one caliper takes 45 hours alone. Although each layer of material cools down immediately and the nest can be laid, the brake calipers contain 2,213 layers of molten ink dust. After the entire caliper has been printed, it must go into the oven at nearly 1.300 degrees Fahrenheit, then it is treatedto ensure a smooth and glossy finish.
Mini.
3D printing even plays a role in the production of the Mini. The British automaker owned by BMW, has recently announced a new programm called “Mini Yours Customized” to launch.
Mini already has a reputation for offering a level of personalisation for cars in the mass market that you can`t get anywhere else. But this new program will get things moving. Mini owners can order completely customized components, such as a light cover or a door threshold with thei name, a favorite phrase or a design that is different from others.
The secret of this next stage vehicle customization is 3D printing. It allows mini-owners to create a unique piece of their car in any color and design to suit their preferences. Owners keep the factory components, so if they want to sell or trade their Mini, they can remove the custom parts.
Large series production.
Despite its advantages, 3D printing technology has not yet reached the point where it is effective for larger production plans. The main focus is on time, as other methods can produce massive quantities of the same part in quick succession.
At the moment it seems that 3D printing is a practice reserved for exotic small series vehicles. As technology improves and print speed increases, automotive manufacturers may be able to make rapid changes to the design of a production vehicle, such as correcting an undetected error or improving a layout based on customer feedback.
Another application in the automotive industry is at an early stage: the production of parts for obscure cars. Jay Leno has said that he uses a 3D printer to replace components on some of this old, unique vehicles. This technology has the potential to satisfy the unmet need in the market for the average car owner.
Basically, their acceptance in the automotive industry will only increase with the time and spread of 3D printers.
If you need assistance modeling your 3D print products, please contact us. We will be happy to help you.